Your Risk Free Way to Find Savings
Wikipedia describes process integration as “A holistic approach to process design which considers the interactions between different unit operations from the outset, rather than optimising them separately.”
Process integration is easy to implement, but modern project management practices (such as vertical contracting) make it difficult to fully implement. Individual technology providers will use process integration to optimise their system, but a facility consisting of several systems will not be holistically optimised.
It is possible to achieve FULL BENEFIT of optimised technology providers AND the holistic benefit of full integration, but issues such as project timing and commercial agreements are significant and sometimes insurmountable barriers.
We can perform numerous process integration studies in the small window of opportunity immediately before commencing FEED. This is the point when most of the key decisions have been made, and this is the last chance for significant front end loading before commencing FEED. The owner should have conditional agreements in place with all technology providers, but no firm agreements.
The basic plan is as follows:
- Agree on the terms and conditions of the study.
- The Owner will develop an economic model of capital and operating costs.
- Owner will commit to technology providers, but the technology provider design is not frozen. This helps to ensure the technology provider will get an order, but there is still some flexibility in the commitment, and the final design can change.
- Technology providers agree to work with other technology providers to incorporate results of integration findings in a way that does not compromise commercially sensitive issues.
- Owner, technology providers, and we will jointly work to ensure all safety and operability issues are addressed.
- We will be given access to key data from the technology providers. We will require all pertinent data relating to the systems to be analysed.
- We will perform the numerical integration analysis. The numerical analysis is FREE of charge. This will determine a threshold of whether to proceed with further analysis.
- At this point, you have benchmarked yourself against yourself. You know what you are doing against what you could be doing.
What exactly is “efficiency”? We have a very simple equation of efficiency, but we are happy to use your definition.
Our definition…
Efficiency = (What you could be using)/(What you are using)
At this point, we may make a proposal on how you can capture these potential savings. Potential savings from an integration study include
- Reduced utility requirements
- Optimised utility header conditions
- Reduction in Capital Expenditure
- Operational Cost Savings
- Emissions Reductions
- Potential for small changes in process conditions to create large savings
An Example Of Our Success
One of our clients used a heat integration analysis to optimise their system. Figure 1 shows the grand composite curve for that optimised system. The client had successfully used process integration techniques on a process design that was frozen. They had successfully met all thermodynamic targets, and the system was considered “optimised”. They had achieved a design that was 100% thermodynamically efficient … within the constraints of their review.
But they did not consider all “soft constraints”. A soft constraint is often in the form of “must be less than” or “shall not exceed”. This one opportunity was all we needed.
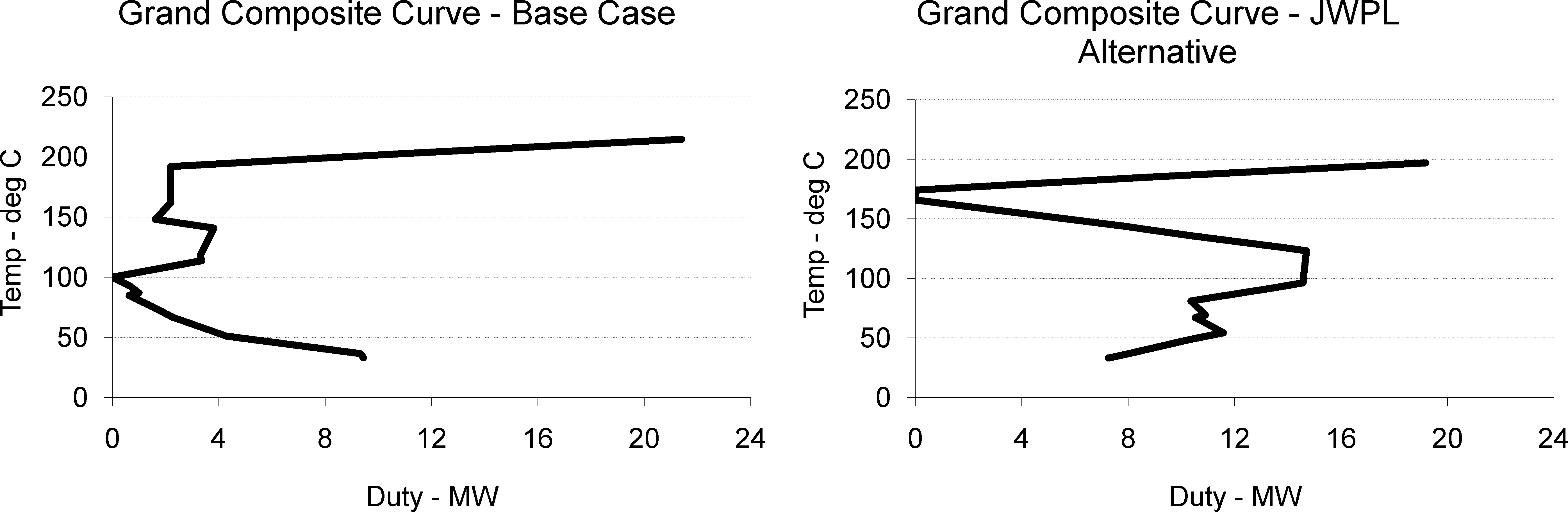
We found one issue had not been fully utilised. We used that issue as the basis for altering the design. The result is shown in Figure 2.
Based on our findings:
- Total hot utility requirements were reduced by about 10%
- Cooling water was not required for steady state operations. A small air cooler was needed for start-up
- The site had two steam headers. Our design reduced higher pressure steam requirements by about 10%, and generated some lower pressure steam instead of consuming cooling water.
In this instance, the client approached us too late to implement these changes, which illustrates the importance of contacting us early in your process development.
In summary, the focus is on identifying any possible improvements that will be in the owner’s best interest.
Please contact us to arrange for your no-risk integration analysis.